Slag pot is one of the important metallurgical containers, which is mainly used to carry converter steel slag, desulphurization slag and ladle casting surplus of continuous casting. However, the stress accumulated in the casting process of the cast steel slag ladle, as well as the harsh working environment, are easy to cause damage to the slag pot and affect its life.
KUNFENG® Foundry has more than ten years experience in slag pot industry and continuously upgraded the technology of production.
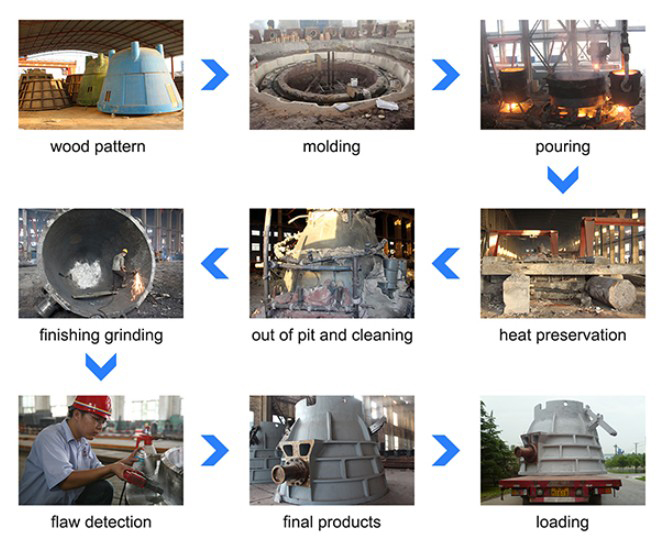
1. Molding
Before pouring, the casting process is digitally simulated by CAE software. And the forming process should be analyzed and predicted, and then the process of slag casting will be optimized continuously.
Complete sets of metallurgical accessories, good overall size control, the use of sodium silicate sand molding process, can prevent the occurrence of hot cracks in castings, while the use of pit modeling, not affected by the season, high production efficiency.
2. Pouring and heat treatment
Proportionally smelt qualified raw and auxiliary materials in the electric arc furnace, and then proceed the spectral analysis of the hot metal sample. After passing the inspection, the raw and auxiliary materials should be poured quickly, and the pouring time and temperature need to be recorded.
In order to solve the problem of large difference in carbon content between earshaft alloy steel and pot carbon steel, KUNFENG® cast steel customized a set of complete process to strictly control the welding problems in the production process.