Pouring is an important link in the whole slag tank casting process, and mastering the pouring process items and strictly controlling every detail has become the key to the production of high quality casting steel slag tank in KUNFENG® heavy steel foundry. The process of molten steel pouring is liquid filling, and the following matters should be paid attention to during the whole pouring process:
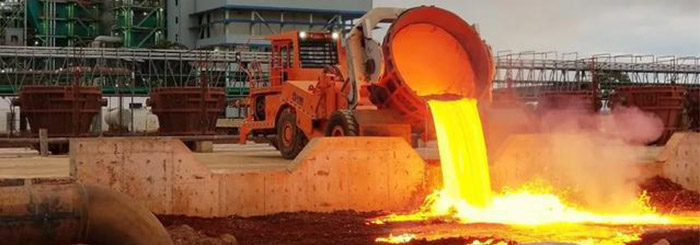
The sprue of Kunfeng casting steel slag tank factory should be full of molten steel from beginning to end, If it doesn't fill up, it is because the strength of the coating layer is not enough, it is easy to set up molding sand to collapse or enter the gas, so that the casting steel slag tank has defects.
The casting steel slag pots should grasp the three principles of stability, accuracy and speed, and the sprue cup can directly achieve fast and uninterrupted flow. For example, when the casting steel slag tank with the same box is poured, the gas will enter when the flow is cut off, which can easily lead to collapse or increase of stomatal defects, serious direct scrap.
Some steel casting factories will use negative pressure closed casting when producing steel slag pots, such as lost foam casting, when the body fluid enters the mold, the plastic will burn and gasify, then there will be a temporary vacancy in the front section. The sprue should be a little farther away from the model of the casting slag tank. If the vertical sprue is used, the lower position of the whole box should be chosen. At the same time of pouring, the vacuum of negative pressure should be controlled within the prescribed range, and after completion, it should be kept under negative pressure for a period of time, so that the molten steel can be cooled and solidified before it can be out of the box.
No matter what kind of large casting Kunfeng casting steel slag tank manufacturers produce, special attention will be paid to pouring, so as to ensure the quality of large steel casting and meet the specific needs of.