The key to maintain steelmaking slag tank is to prevent from: water, excessive moisture in materials (moist materials), excessive moisture in handling equipment, poor slag agitation, excessive feeding speed, excessive material dust, etc.
1. The production area should be kept dry, and water or moisture should be prevented from being present or damp around the slag pit, furnace platform, and equipment.
2. Before using containers for holding molten steel (slag tank, ladle, etc.), check and prevent the presence of water, refractory materials for ladles need to be dried to a certain temperature before receiving materials.
3. Scrap steel added to the furnace should be ensured not to be exposed to rainwater or stored water.
4. Do not throw any debris (especially water-containing beverage bottles, cans, cloth strips, etc.) into the containers for holding molten steel.
5. Cooling equipment needs to be regularly inspected and maintained to prevent water leakage during the working process.
6. After steelmaking and slagging, it is forbidden to put any wet, water-containing, or sealed containers and other debris into the containers for holding molten steel.
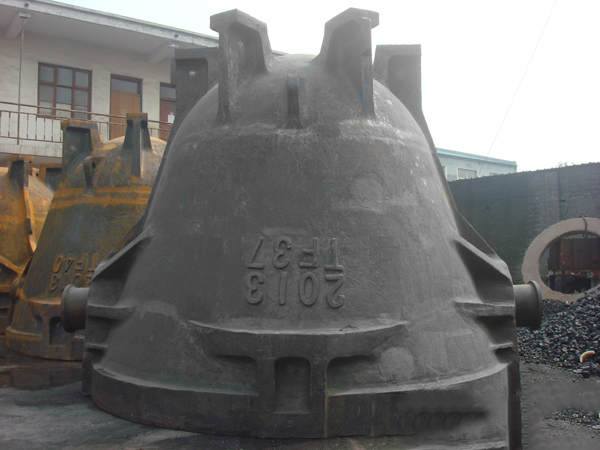
The slag tank is the most important equipment used in the steel making process in the metallurgical industry. It is a container used to hold the slag that is generated due to high temperature s during the steel making process. The two ends of the slag tank have excellent and uniform bowl-like components. The slag tanks produced by our company are relatively small in size compared to the original slag tanks, and they have the characteristics of high pushing force, easy repair, and durable service life.
Slag tanks are commonly found in iron tapping and slag tapping areas. Modern blast furnace iron tapping facilities are equipped with mud guns, slag tanks, cranes, and iron ladles. Modern blast furnaces adopt the method of flushing slag in front of the furnace or setting up dry slag pits. Due to the dust flying during iron tapping, most of them now use blowers and bag filters. After the furnace dust is recovered with lead and zinc, it can be used as material for sintering or pelletizing. Some blast furnaces are also equipped with casting machines. Its metallurgical recovery capacity has also been greatly improved, and it works in collaboration with other equipment to make the operation more smooth.
Contact us to learn more about casting slag pot! We are ready to assist you.